Ultimate Guide to Conformal Coating
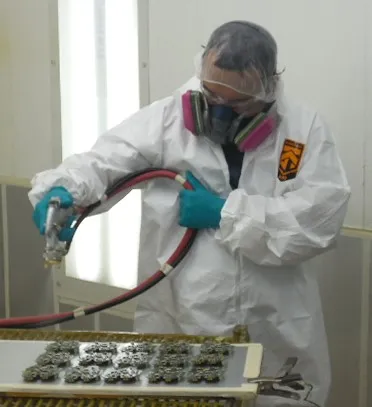
Conformal coating involves applying a thin, protective layer of high-performance polymeric material to printed circuit boards (PCBs) or designated targets. This coating acts as a barrier against various environmental factors such as moisture, dust, corrosion, and more. At Plasma Ruggedized Solutions, we offer adaptable conformal coating variations tailored to meet your specific project requirements, ensuring optimal protection for your electronic assemblies.
Understanding Conformal Coating Methods
Ensuring the desired conformal coating method is compatible with your design goals is essential. We provide adaptable, case-by-case conformal coating variations, from first articles to large production quantities, to match your specific conformal coating needs.
- Learn more about our brush coating process for precise and controlled application.
- Discover our immersion coating solutions for comprehensive coverage and protection.
- Explore our spray coating services for efficient and uniform application.
- Delve into our advanced vapor deposition techniques for superior coating performance.
Choosing the Right Coating Method
Selecting between conformal coating and potting/encapsulation depends on your application requirements. While potting/encasing offers robust protection suitable for high-speed production lines, the conformal coating provides a thinner protective layer ideal for applications where PCB thickness is a concern. Our experts at Plasma Ruggedized Solutions can assist you in determining the most suitable coating method for your project needs. Learn more about potting and encapsulation.
Conformal Coating Selection Services
Our experienced teams collaborate with you to develop tailored solutions for your project, ensuring compatibility, reliability, and cost-effectiveness. From initial design stages to production, Plasma Ruggedized Solutions offers comprehensive engineering services to meet your conformal coating needs.
- Dive deeper into our comprehensive guide for selecting the right conformal coating for your application.
- Explore our versatile coating application techniques tailored to your needs.
When your components or applications aren’t performing as intended, we provide coating removal and stripping services to ensure that the performance of your PCBs is compatible with your application specifications and offers adequate protection.
Industry Standards and Product Testing Services
Our production processes comply with industry standards to ensure the performance of your products meets application requirements. Plasma Ruggedized Solutions holds quality assurance certifications from several regulatory organizations to demonstrate our commitment to pursuing the highest level of quality that meets or exceeds expectations.
Conformal coatings and potting/encapsulation services are FIPS-certified, with Level 1-4 security available to protect electronic devices and assemblies from potential theft or information probing. To provide additional protection for military and defense electronics, we have engineered MIL-SPEC solutions specific to application requirements. IPC recognizes our standardized capabilities for compliance with IPC-CC-830C, IPC-A-610G, and IPC-J-STD-001H:
- IPC-CC-830C: Referring to the primary standard for conformal coatings on PCBs, this specification replaces MIL-I-46058C to denote requirements for material, curing, shelf-life, viscosity, chemical, and appearance, resistance to moisture, fungus, and flammability, as well as electrical specifications.
- IPC-A-610G: Discussing conformal coating coverage and thickness, this specification signifies requirements to ensure the acceptability of electronic assemblies.
- IPC-J-STD-001H: Regarding requirements for soldered electrical components and electronic assemblies, this standard details application, materials, thickness, and uniformity of conformal coatings and encapsulation.
Additionally, we offer a wide range of product screening, testing, and laboratory services to guarantee the quality of your products.
Contact Plasma Ruggedized Solutions for High-Performance Conformal Coating Services
At Plasma Ruggedized Solutions, we aim to provide unmatched quality in conformal coating and potting/encapsulation for electronic components and devices. We are a leader in protective solutions for electronics across industries, delivering certified services and processes that ensure the performance and security of your products.
Contact our expert team with your questions or request a quote to start on your project.